Exploring the Connection Between Crushers and Material Quality
Exploring the Connection Between Crushers and Material Quality
Table of Contents
Introduction to Crushers and Material Quality
Understanding Crushing Processes
Different Types of Crushers and Their Functions
Impact of Crushing on Material Properties
Optimizing Crusher Performance for Quality Output
Maintenance and Its Role in Material Quality
Case Studies and Real-Worl
Jul 02,2025
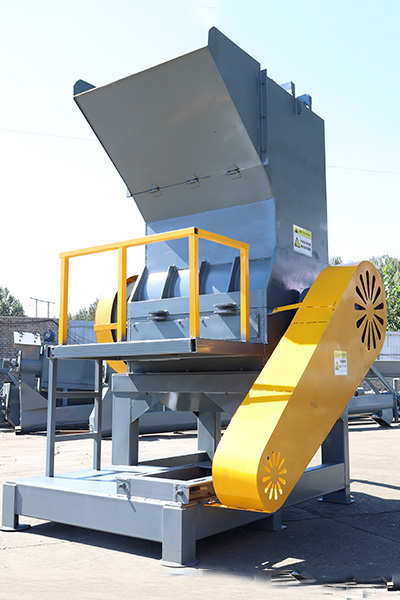
Exploring the Connection Between Crushers and Material Quality
Table of Contents
- Introduction to Crushers and Material Quality
- Understanding Crushing Processes
- Different Types of Crushers and Their Functions
- Impact of Crushing on Material Properties
- Optimizing Crusher Performance for Quality Output
- Maintenance and Its Role in Material Quality
- Case Studies and Real-World Examples
- Future Trends in Crushing Technology
- Frequently Asked Questions
- Conclusion
Introduction to Crushers and Material Quality
The **manufacturing sector** relies heavily on the efficiency and effectiveness of **crushing machinery**. As industries evolve, the demand for high-quality materials has intensified, making it imperative to understand how crushers influence material characteristics. This article explores the connection between crushers and material quality, shedding light on various aspects that affect overall performance.
The role of crushers is pivotal in transforming raw materials into usable products. Understanding this relationship provides manufacturers with insights that can lead to better material quality and enhanced production efficiency.
Understanding Crushing Processes
Crushing is a fundamental process in the manufacturing and mining industries. It involves reducing large rocks or ores into smaller, more manageable pieces. This process can be divided into several stages:
Primary Crushing
In the **primary crushing stage**, large materials are broken down into smaller fragments. This is typically done using **jaw crushers** or **gyratory crushers**, which apply compressive force to reduce material size effectively. The output from this stage is often referred to as "run-of-mine" material, which is further processed in subsequent stages.
Secondary and Tertiary Crushing
Following primary crushing, secondary and tertiary crushers further reduce the size of the material. **Cone crushers** and **impact crushers** are commonly used during these stages. The aim is to produce finer materials that meet specific size and quality requirements.
Different Types of Crushers and Their Functions
Understanding the different types of crushers available is essential for optimizing material quality. Each type of crusher serves a unique function and can impact the material properties differently.
Jaw Crushers
Jaw crushers are primarily used for primary crushing. They operate with a fixed and a movable jaw to crush material by compressive forces. These crushers are particularly effective for hard and abrasive materials.
Impact Crushers
Impact crushers utilize high-speed impact forces to break down materials. They are versatile and can handle a wide range of materials, making them ideal for secondary and tertiary crushing applications.
Cone Crushers
Cone crushers are designed for secondary and tertiary crushing. They are known for their high efficiency and ability to produce finely crushed material with minimal downtime.
Roll Crushers
Roll crushers use two rotating cylinders to crush materials. They are particularly effective for producing uniform particle sizes and are commonly used in coal and mineral processing.
Impact of Crushing on Material Properties
The crushing process significantly affects the physical and chemical properties of materials. Understanding these impacts is critical for ensuring high-quality outputs.
Particle Size Distribution
One of the most crucial aspects affected by crushing is the **particle size distribution**. The size of the crushed material influences its flowability, packing density, and overall performance in subsequent processes. A well-distributed particle size is essential for achieving optimal material quality.
Crushing Strength
Crushing strength refers to the ability of a material to withstand compression without breaking. The crushing process can alter this property, impacting how materials perform under stress. Manufacturers must consider this when selecting crushers and configuring processing parameters.
Chemical Composition
The crushing process can also affect the **chemical composition** of materials. For example, excessive crushing may lead to the alteration of mineral structures, which can impact the material's overall quality and suitability for specific applications.
Optimizing Crusher Performance for Quality Output
To achieve the best material quality, it is essential to optimize crusher performance. Several strategies can be employed to enhance crushing efficiency and product quality.
Proper Equipment Selection
Selecting the right type of crusher for the material being processed is critical. Factors such as material hardness, desired particle size, and throughput capacity should guide equipment choices.
Adjusting Operating Parameters
Operational parameters such as feed rate, crushing speed, and closed-side settings should be continuously monitored and adjusted to maintain optimal performance. Regularly reviewing these parameters allows manufacturers to adapt to varying material characteristics.
Utilizing Advanced Technologies
Incorporating advanced technologies such as automation and predictive maintenance can enhance crushing performance. **Smart sensors** and control systems can provide real-time data, enabling manufacturers to make informed decisions and optimize processes for better material quality.
Maintenance and Its Role in Material Quality
Proper maintenance of crushing machinery is crucial for ensuring consistent material quality. Neglecting maintenance can lead to equipment failures and subpar output.
Regular Inspections
Conducting regular inspections helps identify potential issues before they escalate. Routine checks on wear parts, lubrication systems, and overall equipment condition can prevent downtime and maintain performance levels.
Scheduled Maintenance Programs
Implementing scheduled maintenance programs ensures that equipment operates at peak efficiency. These programs should include detailed checklists and timelines for servicing critical components.
Training Personnel
Training operators and maintenance personnel on best practices is essential for maximizing equipment lifespan and performance. Well-trained staff can detect early signs of wear and adapt operations to maintain high material quality.
Case Studies and Real-World Examples
Examining real-world case studies can provide valuable insights into how the connection between crushers and material quality plays out in practice.
Case Study 1: Quarry Optimization
A leading quarry implemented a new jaw crusher tailored to their specific material characteristics. By optimizing the feed rate and regularly adjusting the closed-side settings, they significantly improved their particle size distribution, resulting in higher-quality aggregates.
Case Study 2: Recycling Facility Upgrade
A recycling facility upgraded its impact crushers to handle a broader range of materials. They also integrated smart sensors to monitor performance metrics. The result was reduced downtime and improved material quality, leading to increased customer satisfaction.
Future Trends in Crushing Technology
As industries continue to evolve, so does crushing technology. Staying informed about future trends is vital for maintaining a competitive edge.
Automation and Smart Technologies
The adoption of automation and smart technologies will revolutionize crushing processes. Predictive analytics and machine learning will enable manufacturers to optimize performance continuously and adapt to changing material characteristics.
Sustainability Initiatives
Sustainability is becoming increasingly important in manufacturing. New crushing technologies will focus on reducing waste and energy consumption, ensuring that material quality does not come at the expense of environmental responsibility.
Frequently Asked Questions
What role do crushers play in material quality?
Crushers are essential in reducing raw materials to usable sizes, profoundly affecting their physical and chemical properties, ultimately influencing material quality.
How does particle size distribution impact material performance?
A well-distributed particle size enhances flowability and packing density, which are crucial for the performance of materials in various applications.
What are the best practices for maintaining crushers?
Regular inspections, scheduled maintenance programs, and personnel training are critical for maintaining crushers and ensuring consistent material quality.
What types of crushers are best for specific materials?
The choice of crusher depends on the material's hardness, desired particle size, and throughput requirements. Jaw, impact, cone, and roll crushers each serve different functions.
How can technology improve crushing efficiency?
Incorporating automation, smart sensors, and real-time monitoring can enhance crushing efficiency and material quality by allowing for data-driven decision-making.
Conclusion
Understanding the connection between crushers and material quality is imperative for manufacturers looking to enhance their production processes. By exploring different types of crushers, optimizing performance, and maintaining equipment, companies can ensure they produce high-quality materials. As technology advances, staying informed about the latest trends will further empower manufacturers to achieve excellence in material quality. Embracing these insights will lead to improved efficiency, sustainability, and customer satisfaction in the ever-evolving manufacturing landscape.
TAG:
Contact Us
E-mail :
Phone/WhatsApp:
Address:
Shunping, Baoding City, Hebei Province